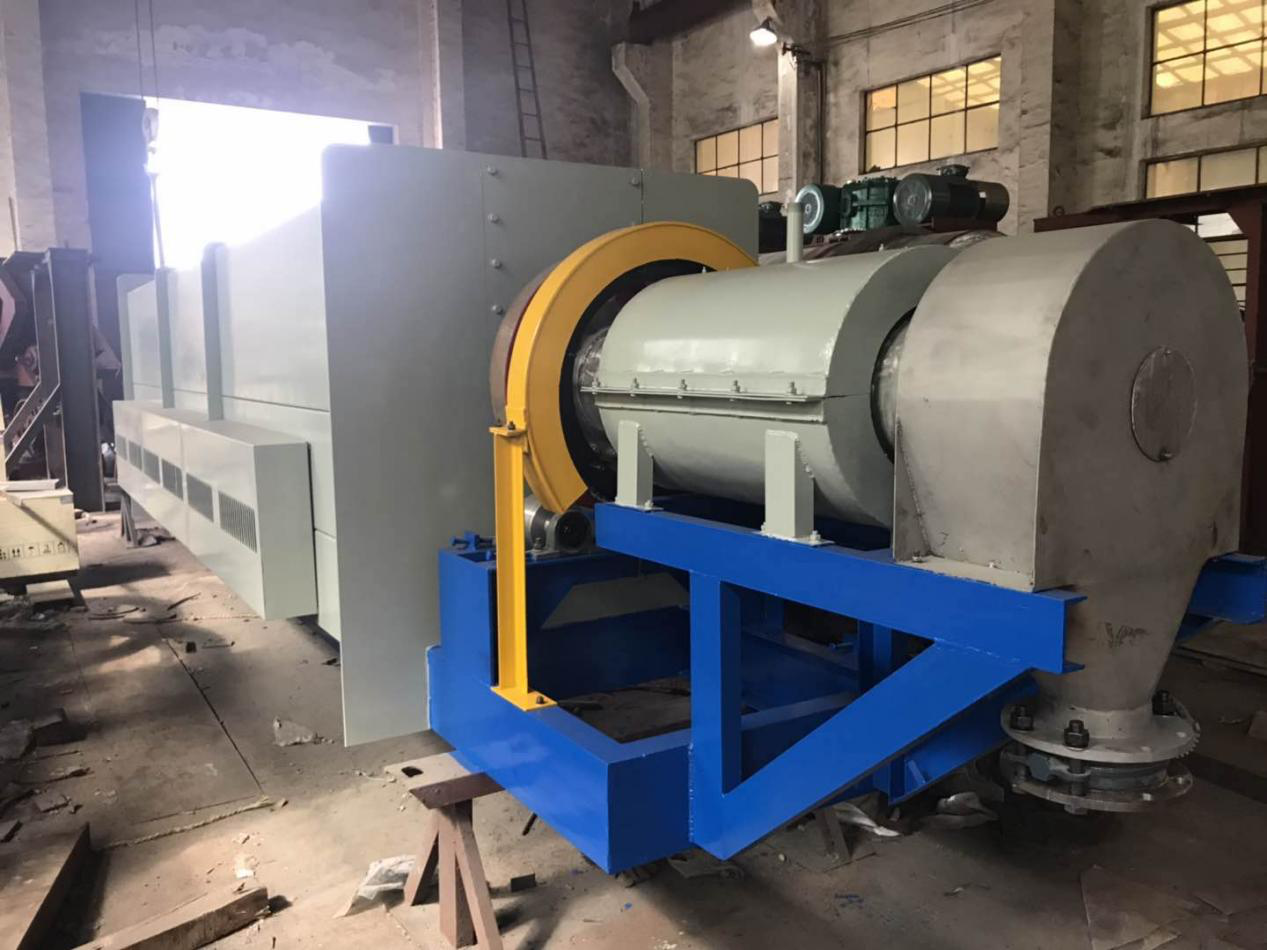
物料的干燥与脱水:在许多生产过程中,进入回转窑的物料往往含有一定水分。例如,在水泥生产中,黏土、石灰石等原料可能因储存或开采条件而含有部分水分。高温环境能快速蒸发物料中的水分,实现干燥与脱水。一般来说,回转窑前段温度通常在200-500℃,这个温度区间足以使物料中的游离水迅速蒸发。水分的去除对于后续的煅烧等工艺至关重要,因为水分的存在会影响物料的传热效率,增加能耗,并且过多水分可能导致物料在窑内形成团聚,影响反应的均匀性。
物料的熔化与融合:对于一些需要将不同原料熔合在一起的工艺,如炼钢过程中矿石与熔剂的融合,高温环境必不可少。在高温下,物料达到熔点后开始熔化,不同成分相互融合,形成均匀的液相。以玻璃制造为例,各种矿物原料如石英砂、纯碱、石灰石等,在回转窑内1500-1700℃的高温下,会逐渐熔化并融合成均匀的玻璃液。这种均匀的液相对于保证产品质量的稳定性和一致性至关重要。如果温度不足,物料无法充分熔化与融合,会导致产品内部出现杂质、不均匀等缺陷,严重影响产品性能。
二、推动物料的化学反应
分解反应的进行:回转窑常用于一些化合物的分解反应。比如在水泥生产的熟料煅烧过程中,碳酸钙(CaCO?)需要在高温下分解为氧化钙(CaO)和二氧化碳(CO?)。这一分解反应的温度通常在800-1000℃左右。只有在这样的高温环境下,碳酸钙分子才能获得足够的能量克服化学键的束缚,发生分解。若温度达不到要求,碳酸钙分解不完全,会导致熟料中游离氧化钙含量过高,影响水泥的安定性,使水泥制品在使用过程中出现膨胀、开裂等问题。
固相反应的加速:在许多材料生产过程中,固相反应是形成产品关键成分的重要环节。例如在陶瓷生产中,各种矿物原料在回转窑内通过固相反应形成具有特定性能的陶瓷相。高温能够增加固体颗粒表面原子的活性,使它们更容易扩散并与其他颗粒发生反应。一般来说,高温能显著加快固相反应速度,缩短反应时间,提高生产效率。在1200-1400℃的高温下,陶瓷原料之间的固相反应能够较为充分地进行,形成均匀、致密的陶瓷结构,从而保证陶瓷产品具有良好的机械性能、热稳定性和化学稳定性。
三、满足生产工艺与设备运行需求
提高传热效率:回转窑内的高温环境有利于提高传热效率。在高温下,热量传递的方式主要以辐射传热为主,辐射传热的效率远高于传导和对流传热。窑内高温的火焰和物料表面之间通过辐射传递大量热量,使物料能够快速吸收热量,实现快速升温。这种高效的传热方式对于保证物料在窑内短时间内完成物理化学变化至关重要。例如在冶金行业的有色金属冶炼中,需要快速将矿石加热到反应温度,高温环境下的高效传热能够满足这一需求,提高冶炼效率。
维持窑体的正常运行:回转窑的正常运行需要在高温环境下保持窑体的结构稳定性。窑衬材料在高温下能够保持良好的强度和抗侵蚀性能,从而保护窑体金属外壳不受高温物料和火焰的侵蚀。同时,高温环境下窑内气体的流动状态也更加稳定,有利于物料在窑内的均匀分布和顺畅移动。如果温度过低,窑衬材料的性能可能无法充分发挥,导致窑衬过早损坏,增加维修成本和停机时间。而且温度波动较大时,窑内气体流动紊乱,会影响物料的输送和反应的均匀性,进而影响产品质量。
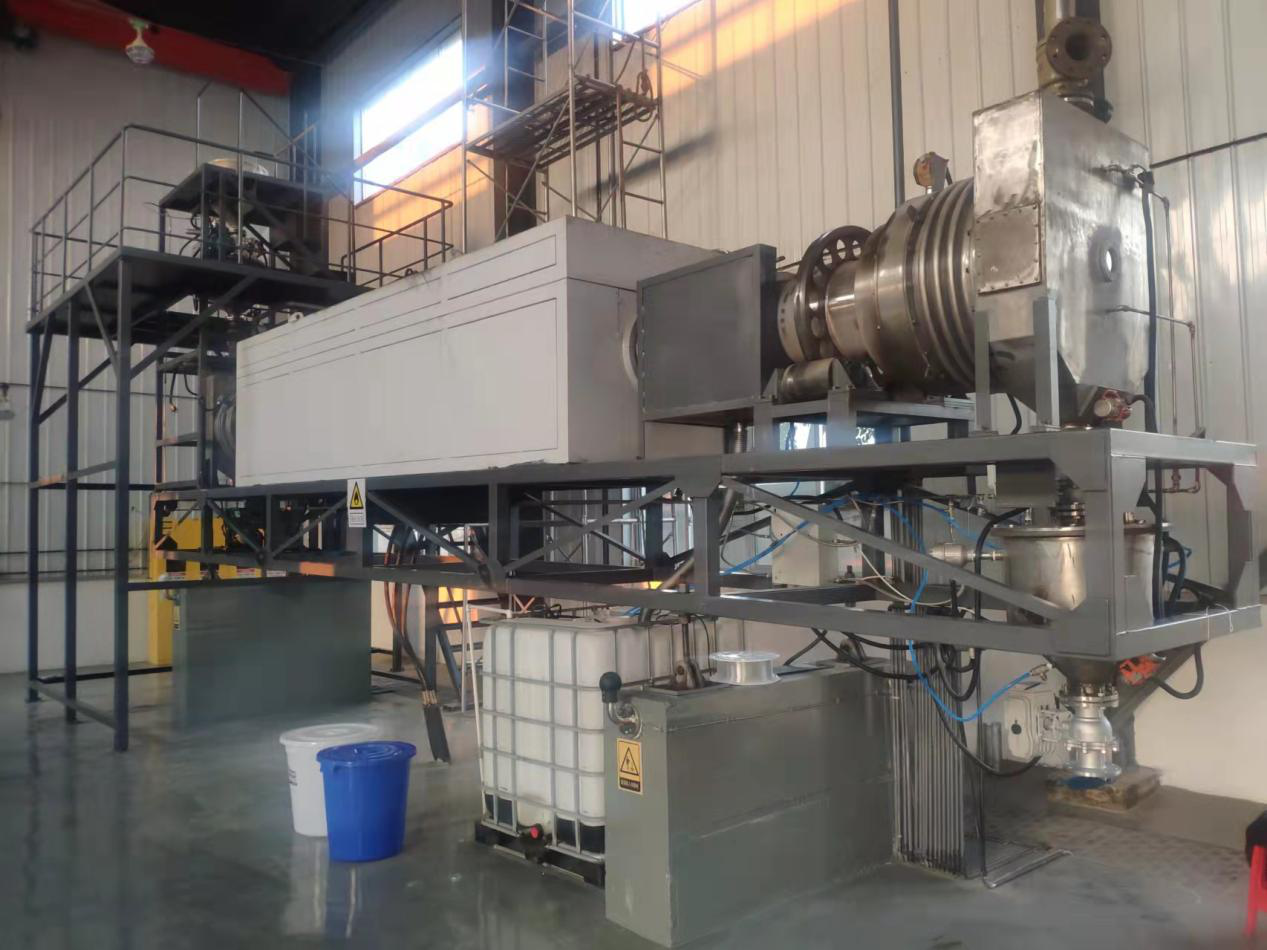
综上所述,回转窑需要高温环境是为了促进物料的物理变化、推动化学反应的进行以及满足生产工艺和设备运行的需求。高温环境是回转窑实现高效、稳定生产,保证产品质量的关键因素。对回转窑高温环境的精准控制和优化,是提高生产效率、降低能耗、提升产品品质的重要途径。感谢阅读,想了解更多欢迎继续阅读《回转窑制造厂家有哪些,回转窑制造厂家排行榜》。