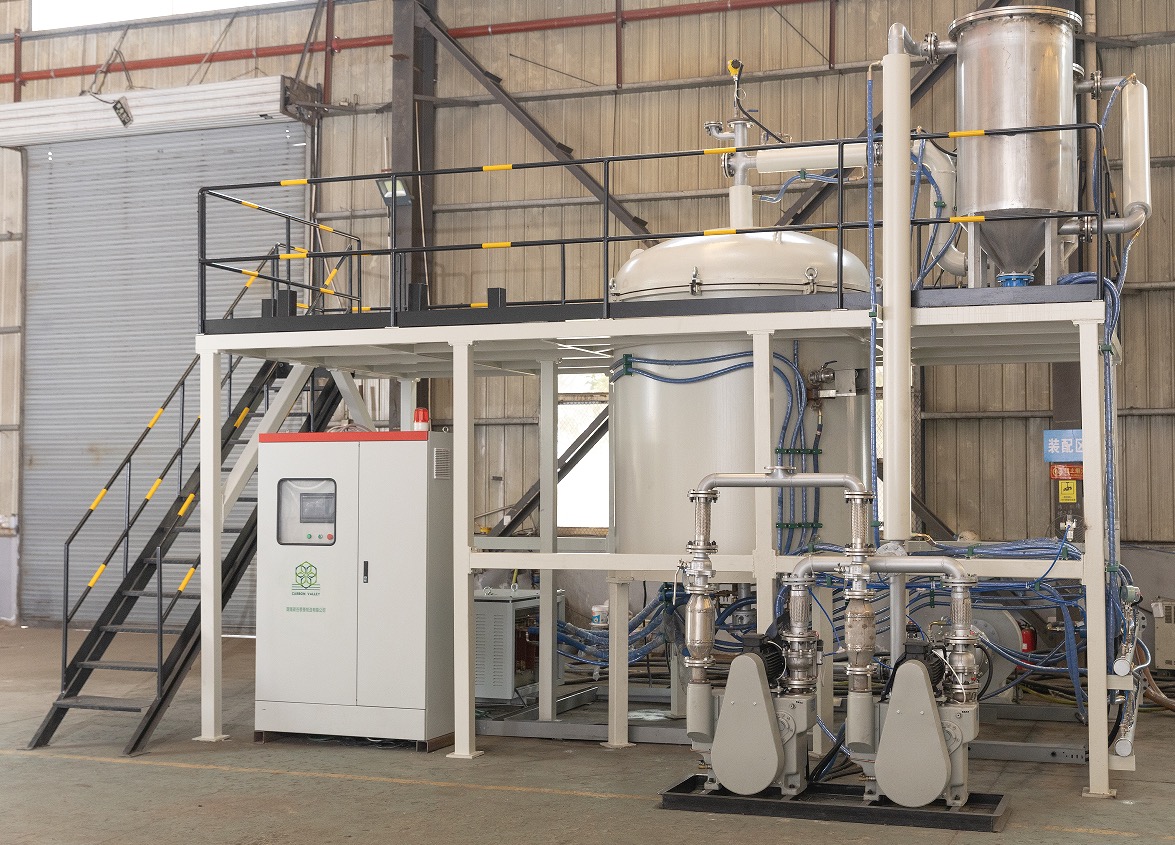
一、压力控制系统组成
真空获得系统
由机械泵(极限真空10^-1 Pa)和分子泵(极限真空10^-4 Pa)组成二级抽气系统,通过PID算法实现抽速调节。最新设备采用磁悬浮分子泵,将抽气效率提升30%。
压力传感系统
配备电容式薄膜规(精度±0.08%)和电离规(量程10^-5至10^2 Pa),双传感器冗余设计确保测量可靠性。智能温度补偿算法可将漂移控制在0.01%/℃以内。
气路调节系统
采用质量流量控制器(MFC)和电动针阀联动控制,气体流量调节精度达±0.5%F.S.,响应时间<100ms。先进设备配备前馈-反馈复合控制算法。
二、关键控制技术
动态平衡控制
通过实时比较设定压力与实测压力差值,自动调节进气阀开度和抽气速率。现代系统可实现±0.5%的压力波动控制。
多区段压力编程
支持多达20个压力控制段设定,各段可独立设置压力值、变化速率和保持时间,满足复杂工艺需求。
异常压力处理
内置压力突变检测算法,当压力波动超过设定阈值时,自动启动应急程序,保护沉积过程不受干扰。
三、工艺参数优化
基础压力控制
典型镀膜工艺要求本底真空≤5×10^-3 Pa,采用阶梯式抽气策略,避免样品放气污染。
工作压力范围
根据不同工艺需求灵活调节:
PVD:0.1-10 Pa
CVD:10^2-10^4 Pa
ALD:10^-1-10^2 Pa
压力-温度协同
开发压力-温度耦合控制模型,确保在升温过程中维持稳定的动力学条件。实验显示该技术可将膜厚均匀性提高15%。
四、最新技术进展
人工智能控制
采用深度学习算法预测压力波动趋势,提前进行调节。某型号设备应用后,压力稳定性提升40%。
数字孪生技术
通过虚拟仿真优化压力控制参数,缩短工艺开发周期。实测显示调试时间可减少60%。
物联网远程监控
5G技术实现设备压力参数的实时云端监测,专家系统可自动诊断异常并提供解决方案。
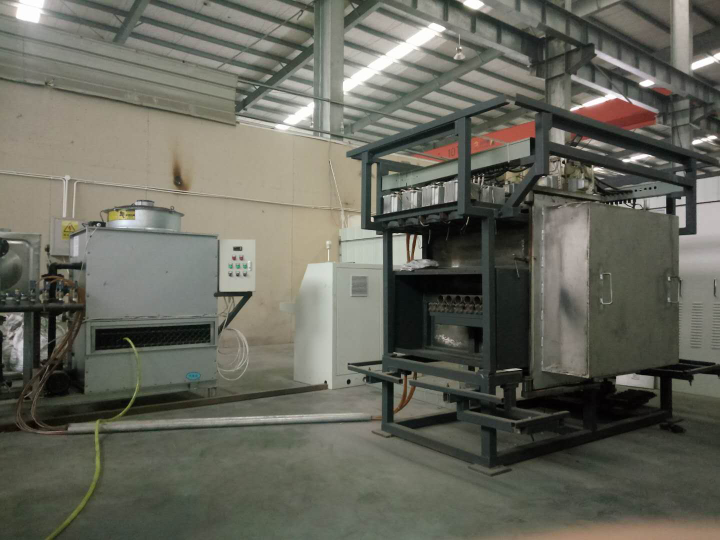
综上所述,气相沉积炉的压力控制是涉及机械、电子、软件等多学科的系统工程。随着智能控制技术的发展,现代设备已能实现±0.2%的压力控制精度。在实际操作中,需要根据具体工艺要求,合理设置压力参数,并定期校准传感器和维护真空系统,才能确保最佳的镀膜效果。感谢阅读,想了解更多欢迎继续阅读《气相沉积炉多少钱,2025气相沉积炉价格》。