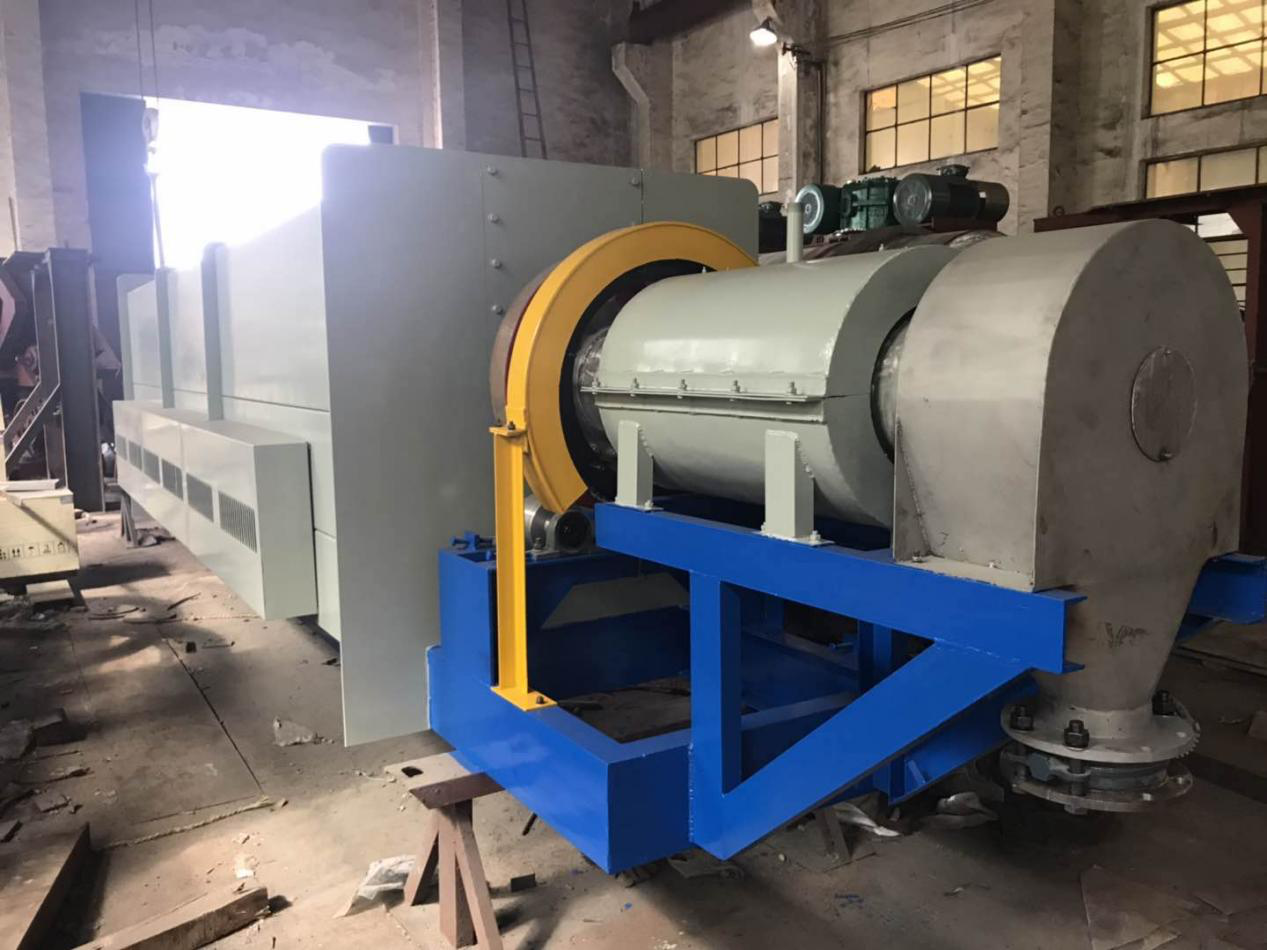
钢材的选用:高温回转窑的筒体、托轮、挡轮等主要部件通常采用优质的钢材制造。筒体作为回转窑的核心部件,需要承受高温、高压以及物料的磨损,因此一般选用具有良好耐热性、耐磨性和高强度的低合金耐热钢,如Q345R、15CrMoR等。这些钢材在高温环境下仍能保持较好的力学性能,确保筒体在长期运行过程中不会发生变形、破裂等问题。托轮和挡轮则需要承受较大的压力和摩擦力,一般选用中碳钢或合金结构钢,如45#钢、40Cr等,通过适当的热处理工艺,提高其表面硬度和耐磨性。
耐火材料的选择:高温回转窑内部需要砌筑耐火材料,以保护筒体免受高温侵蚀,并提高热效率。耐火材料的选择根据回转窑的使用温度、物料特性等因素而定。对于一般的水泥回转窑,常用的耐火材料有高铝砖、镁铬砖、硅莫砖等。高铝砖具有较高的耐火度和机械强度,能承受一定的高温和物料冲刷;镁铬砖则具有良好的抗侵蚀性和高温稳定性,适用于高温、强侵蚀性的环境;硅莫砖具有低导热性和高抗热震性,能有效减少热量散失,提高回转窑的热效率。在选择耐火材料时,还需要考虑其与筒体的粘结性、热膨胀系数等因素,确保耐火材料在使用过程中不会脱落、开裂。
原材料的检验:为了确保高温回转窑的制作质量,对原材料进行严格的检验是必不可少的环节。钢材在进厂时,需要进行化学成分分析、力学性能测试、金相组织检验等,确保钢材的各项指标符合设计要求。对于耐火材料,要检验其耐火度、荷重软化温度、抗热震性、体积密度等性能指标,只有合格的耐火材料才能用于回转窑的砌筑。例如,通过对钢材的拉伸试验,检测其屈服强度、抗拉强度等力学性能;通过对耐火材料的荷重软化温度测试,了解其在高温和一定压力下的变形情况,保证原材料的质量可靠性。
二、零部件的加工制造
筒体的卷制与焊接:筒体的制作通常采用卷制工艺,将钢板按照设计尺寸切割成合适的长度和宽度,然后在卷板机上进行卷制,使其形成圆筒状。在卷制过程中,要严格控制筒体的圆度、直线度和壁厚偏差,确保筒体的尺寸精度。卷制完成后,进行筒体的焊接。焊接工艺是筒体制作的关键环节,需要采用先进的焊接设备和工艺,如埋弧焊、气体保护焊等,确保焊缝的质量。焊接过程中,要对焊缝进行严格的质量检测,包括外观检查、无损探伤等,防止出现焊缝裂纹、气孔、夹渣等缺陷。例如,通过X射线探伤检测焊缝内部是否存在缺陷,确保焊缝的质量符合标准要求。
托轮与挡轮的加工:托轮和挡轮的加工精度直接影响到回转窑的运行稳定性。托轮和挡轮一般采用锻造工艺制造毛坯,然后进行机械加工。在加工过程中,要保证托轮和挡轮的表面粗糙度、尺寸精度和形位公差符合设计要求。例如,托轮的外圆表面需要进行磨削加工,使其表面粗糙度达到Ra0.8-Ra1.6μm,以减小托轮与筒体之间的摩擦力;同时,要保证托轮的圆柱度、同轴度等形位公差在规定范围内,确保托轮在运行过程中受力均匀,避免出现偏磨现象。
传动装置的制造:传动装置是高温回转窑的重要组成部分,包括电机、减速机、联轴器、小齿轮等部件。电机和减速机一般选用标准的产品,根据回转窑的功率和转速要求进行选型。联轴器用于连接电机、减速机和小齿轮,传递动力,其制造精度和安装精度对传动效率和稳定性有重要影响。小齿轮与筒体上的大齿圈啮合,驱动筒体旋转,小齿轮的加工精度和热处理工艺直接影响其使用寿命和传动性能。在制造小齿轮时,要采用高精度的加工设备和先进的热处理工艺,如渗碳淬火、氮化处理等,提高小齿轮的表面硬度和耐磨性,确保传动装置的可靠运行。
三、设备的装配与调试
部件的预装配:在高温回转窑正式装配之前,需要对各个部件进行预装配,检查部件之间的配合精度和安装尺寸是否符合要求。预装配过程中,要对筒体、托轮、挡轮、传动装置等部件进行模拟安装,发现问题及时进行调整和改进。例如,在预装配托轮和挡轮时,要检查托轮与筒体的接触情况,确保托轮与筒体之间的接触均匀,避免出现局部受力过大的现象;同时,要检查传动装置的安装精度,保证小齿轮与大齿圈的啮合间隙和齿面接触面积符合设计要求。
整体装配:在部件预装配合格后,进行高温回转窑的整体装配。整体装配按照从下往上、从内往外的顺序进行,先安装基础底座,然后依次安装托轮、挡轮、筒体、传动装置等部件。在装配过程中,要严格控制各部件的安装位置和垂直度,确保回转窑的整体安装精度。例如,筒体的安装要保证其中心线的直线度和水平度,误差控制在规定范围内,以保证筒体在运行过程中平稳转动;传动装置的安装要保证其与筒体的同心度,避免出现传动不稳定的情况。
调试与试运行:高温回转窑装配完成后,需要进行调试和试运行。调试过程中,要对回转窑的各项性能指标进行检测和调整,包括筒体的转速、托轮的受力情况、传动装置的运行情况、温度分布等。通过调试,确保回转窑的各项性能指标符合设计要求。试运行阶段,要对回转窑进行空载和负载试运行,检查回转窑在不同工况下的运行稳定性和可靠性。在试运行过程中,要密切关注设备的运行状态,及时发现并解决出现的问题,如振动、噪声、温度过高等,确保回转窑能够正常投入使用。
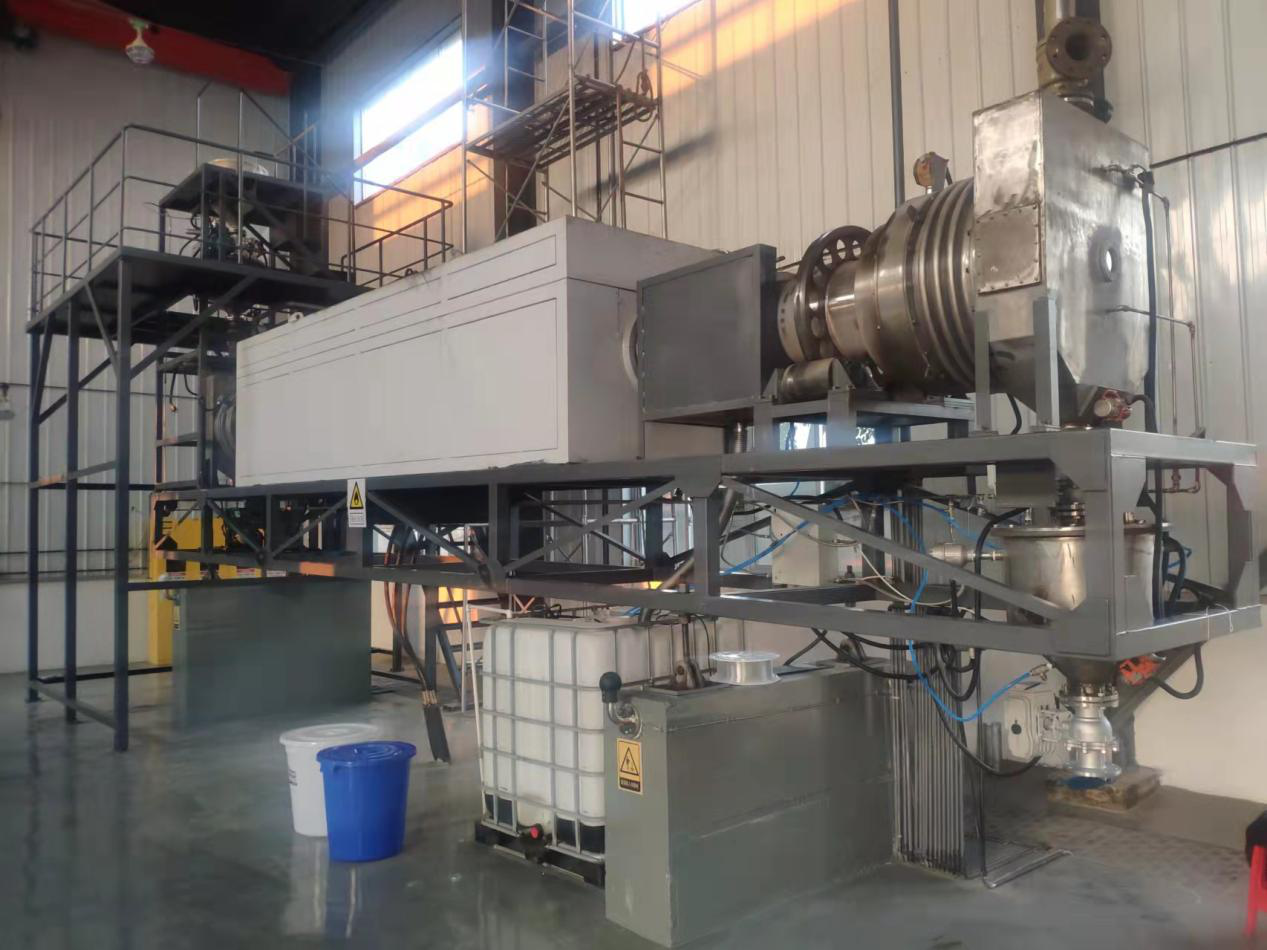
综上所述,高温回转窑的制作工艺涵盖了原材料选择、零部件加工制造、设备装配与调试等多个环节,每个环节都需要严格控制质量,采用先进的工艺和技术,确保回转窑的性能和质量,满足工业生产的需求。随着科技的不断进步,高温回转窑的制作工艺也在不断创新和改进,为相关行业的发展提供更加高效、可靠的设备支持。感谢阅读,想了解更多欢迎继续阅读《高温回转窑热损失高有哪些原因,看完你就知道》。