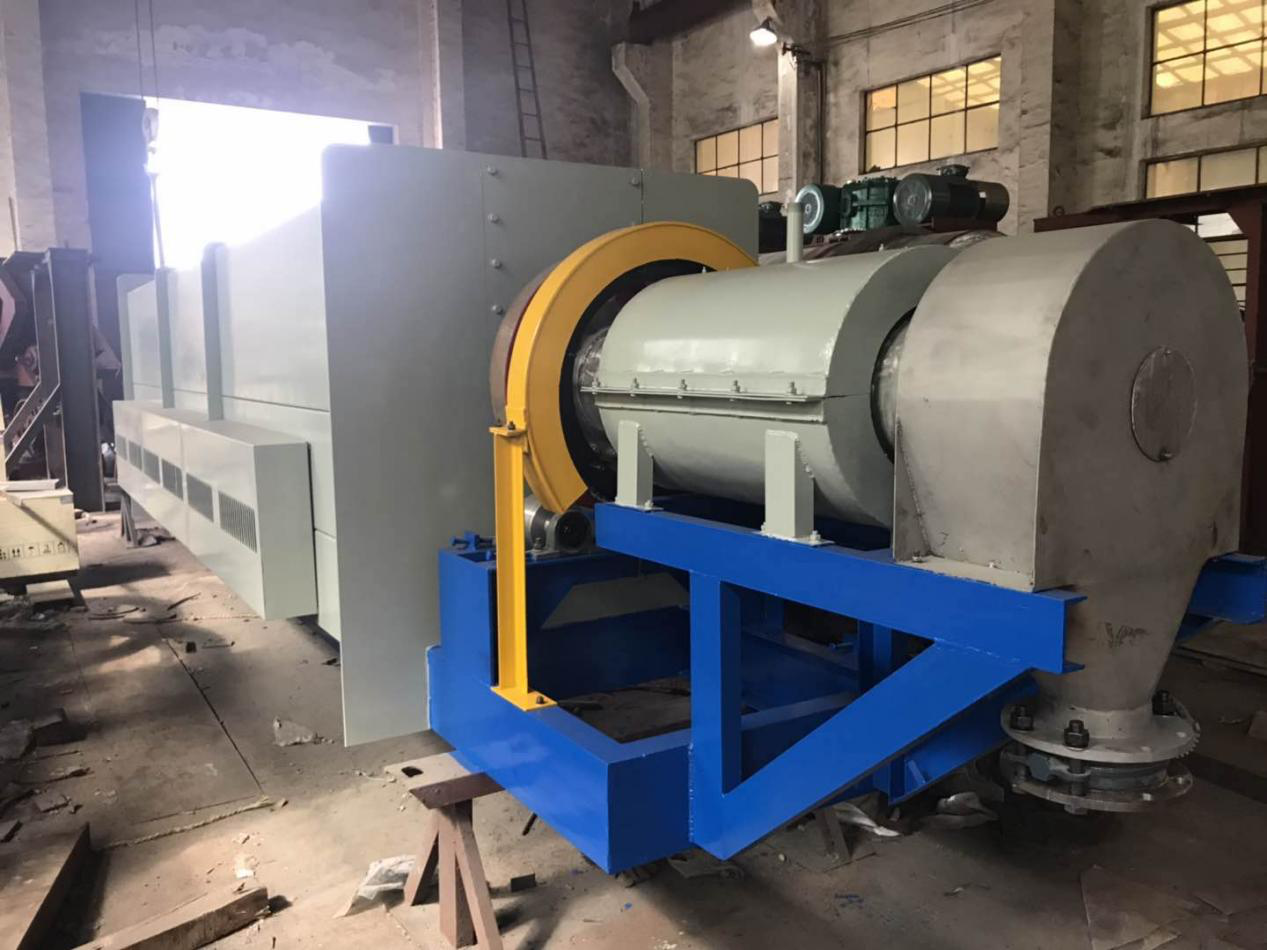
窑体密封不佳:高温回转窑的窑头和窑尾是与外界环境接触较为频繁的部位,如果密封装置出现损坏或者设计不合理,就会导致大量冷空气进入窑内。冷空气的进入会降低窑内的温度,使得燃料需要更多的热量来维持窑内的高温环境,从而造成热损失增加。例如,密封材料老化、磨损,密封结构的间隙过大等情况,都会使窑体的密封性变差。在一些水泥生产企业中,由于没有及时更换窑头密封装置的密封片,导致冷空气大量涌入,经过检测,热损失较正常情况增加了10%-15%。
保温层损坏或厚度不足:窑体的保温层对于减少热量散失起着关键作用。保温层的主要作用是阻止窑内热量向外界传递,如果保温层出现损坏,如出现裂缝、脱落等情况,热量就会通过这些破损部位大量散失。另外,若保温层的厚度不足,其隔热效果也会大打折扣。在一些小型企业中,为了降低成本,采用了厚度较薄的保温材料,或者在安装保温层时施工质量不达标,导致保温效果不佳。经测试,保温层厚度不足的回转窑,热损失比正常情况高出20%-30%。
二、燃烧过程与燃料相关因素
燃料燃烧不充分:燃料在窑内的燃烧情况直接影响着热效率。如果燃料燃烧不充分,一部分燃料的化学能就无法完全转化为热能,而是以未燃烧的形式排出窑外,造成能源浪费。燃料燃烧不充分的原因可能有多种,比如燃料与空气的混合比例不当,当空气供给量不足时,燃料无法完全燃烧;或者燃烧器的性能不佳,不能使燃料充分雾化和分散,导致燃烧不均匀。在一些石灰生产厂中,由于燃烧器老化,燃料燃烧不充分,使得热损失明显增加,同时还会导致产品质量下降。
燃料质量不稳定:燃料的质量对燃烧过程和热损失也有很大影响。如果燃料的热值不稳定,忽高忽低,会导致窑内温度波动较大。为了维持稳定的窑内温度,操作人员需要不断调整燃料的供给量,这就容易造成燃料的浪费和热损失的增加。此外,燃料中杂质含量过高,如煤炭中的灰分、硫分等,不仅会降低燃料的热值,还会在燃烧过程中产生一些不利于燃烧的物质,影响燃烧效果,进而增加热损失。
三、生产操作与工艺控制问题
窑内温度控制不合理:窑内温度的稳定对于热效率至关重要。如果窑内温度过高,会使物料过度反应,同时也会导致热量大量散失;而温度过低,则会使反应不完全,延长生产时间,同样增加了热损失。在实际生产中,由于操作人员对温度控制的经验不足,或者温度监测设备不准确,常常会出现窑内温度波动较大的情况。例如,在某些冶金行业的回转窑生产中,由于温度控制不当,热损失比正常情况高出15%-20%。
物料停留时间不当:物料在回转窑内的停留时间需要根据生产工艺和物料特性进行合理控制。如果物料停留时间过短,物料反应不完全,需要再次进行处理,增加了能源消耗;而停留时间过长,会导致物料过度受热,热量浪费严重。例如,在水泥熟料生产过程中,若物料在窑内停留时间过长,会使熟料的质量下降,同时热损失也会明显增加。
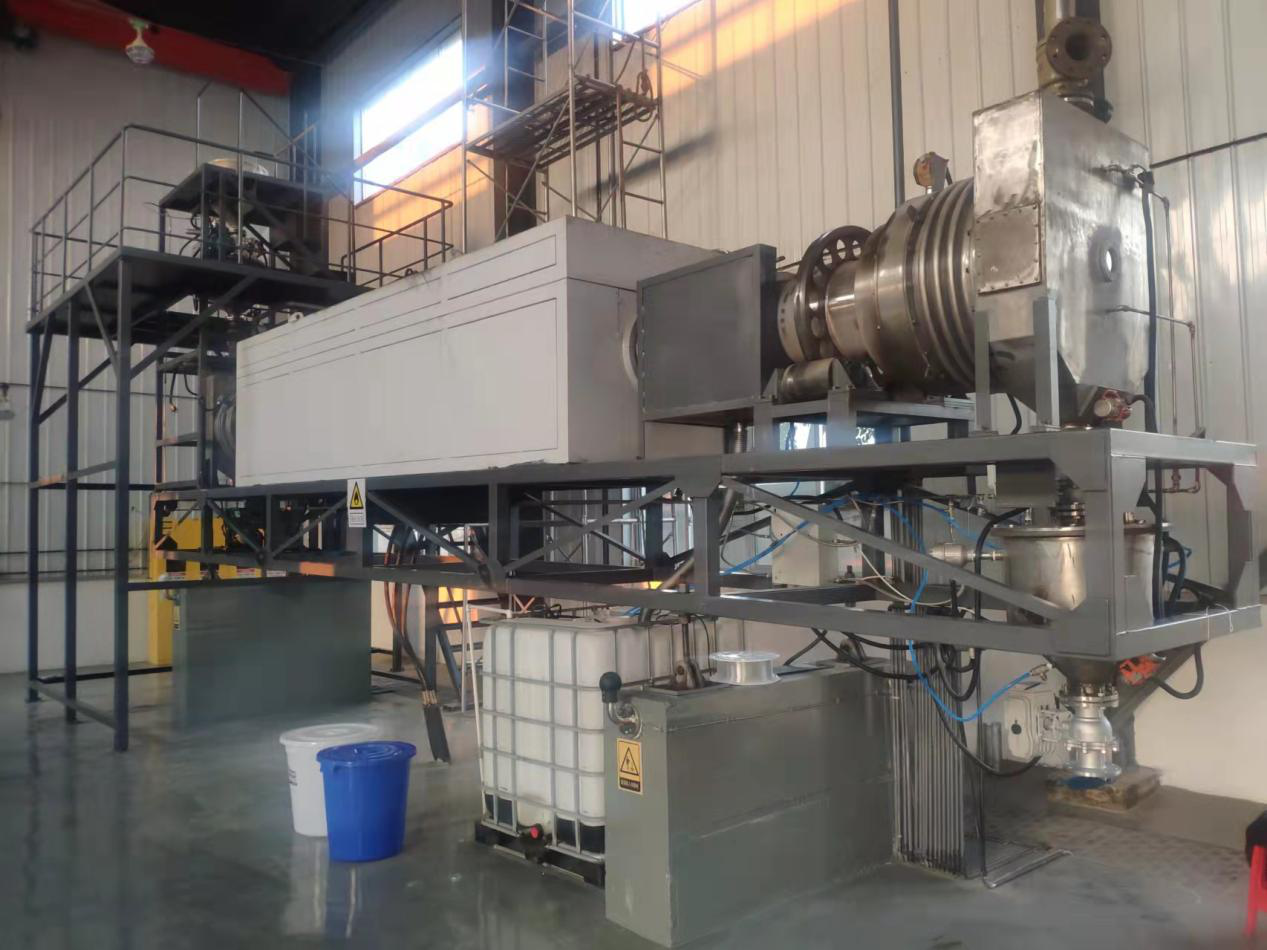
综上所述,高温回转窑热损失高是由多种因素共同作用导致的。从窑体结构、燃烧过程到生产操作等各个环节,任何一个方面出现问题都可能引发热损失增加。企业需要针对这些问题进行全面排查和分析,采取相应的改进措施,以降低热损失,提高高温回转窑的热效率和生产效益。感谢阅读,欢迎继续阅读《高温回转窑最高能承受多高温度,回转窑厂家告诉你》。