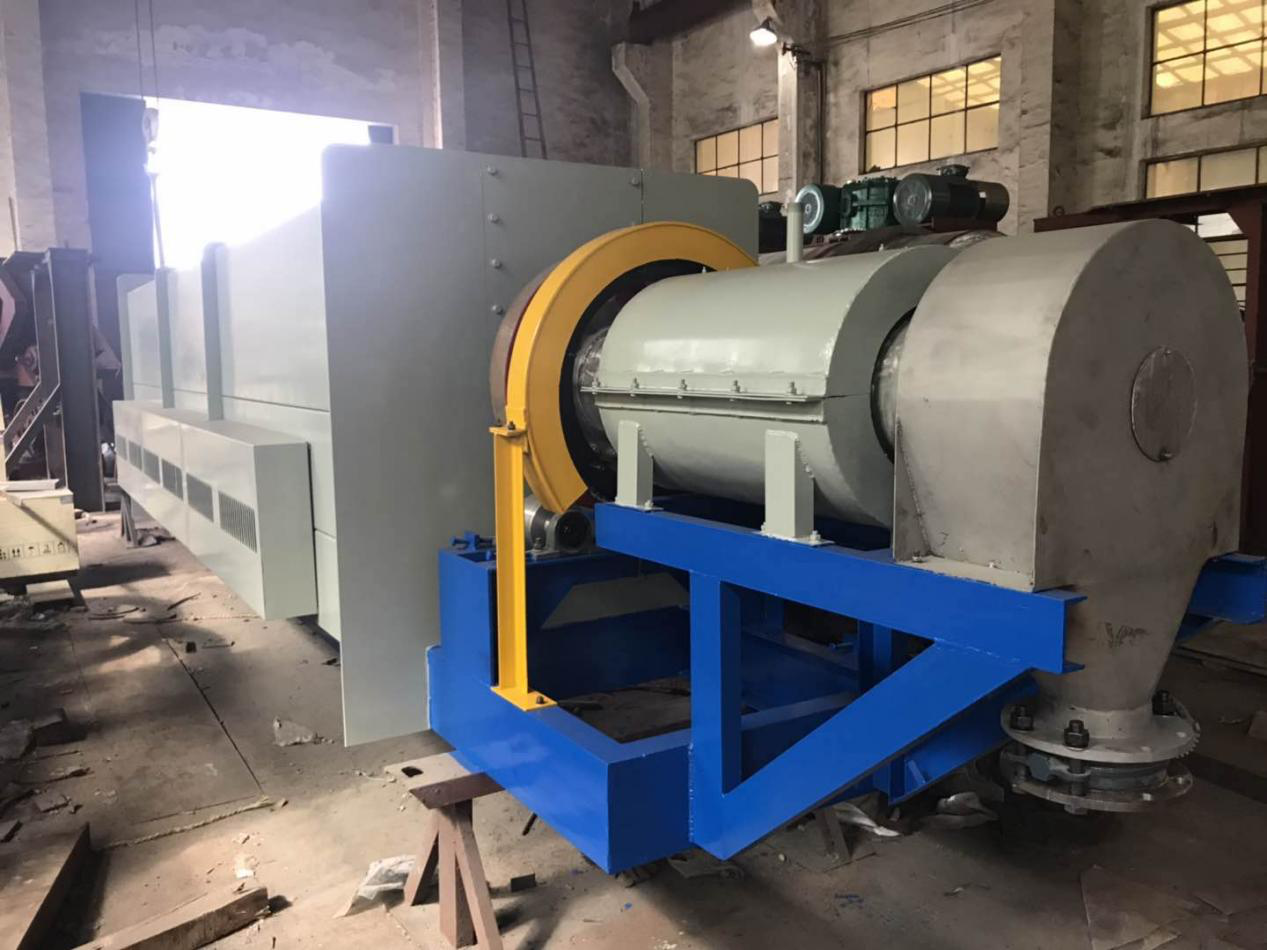
燃料燃烧是回转窑产生高温的主要方式。优化燃料燃烧,提高热量传递效率是提高窑内温度的基础。首先,企业应选择合适的燃料。在我国,煤炭是最常用的燃料,但煤炭的种类繁多,热值、燃烧特性等差异较大。企业应根据实际需求,选择合适的煤炭种类。同时,要保证燃料的充分燃烧,还需对燃烧设备进行优化,如提高燃烧器的性能、改进烟道设计等。
案例:某水泥厂在优化燃料燃烧后,采用高热值煤炭,燃烧器性能得到显著提升,窑内温度提高了 50℃,熟料产量增加了 15%,取得了显著的经济效益。
二、改进窑内结构,提高热交换效率
回转窑内部结构的设计对窑内温度有着直接影响。优化窑内结构,提高热交换效率是提高窑内温度的关键。企业应根据生产需求,对窑内衬砖、隔热层等进行优化设计,提高热量传递速度。此外,还可以采用先进的冷却技术,如喷雾冷却、气幕冷却等,降低窑内温度梯度,提高热交换效率。
三、加强设备维护,保证窑内运行稳定
设备维护是保证高温回转窑窑内温度稳定的重要环节。企业应定期对窑进行检修,保证窑体、窑衬等部件的完好无损。同时,还要加强窑内运行参数的监测,如温度、压力、流量等,及时发现并处理异常情况,保证窑内运行稳定。
案例:某钢铁厂加强对回转窑的维护保养,窑内温度稳定提高了 100℃,生产效率得到显著提升,为企业带来了丰厚的经济效益。
四、实施智能化改造,提升窑内温度控制水平
随着智能制造技术的发展,高温回转窑的智能化改造已成为提高窑内温度的新趋势。企业可利用大数据、物联网等技术,对窑内温度进行实时监测和智能调控,提高窑内温度的稳定性。此外,智能化改造还能为企业提供精准的数据支持,帮助企业优化生产过程,降低能耗。
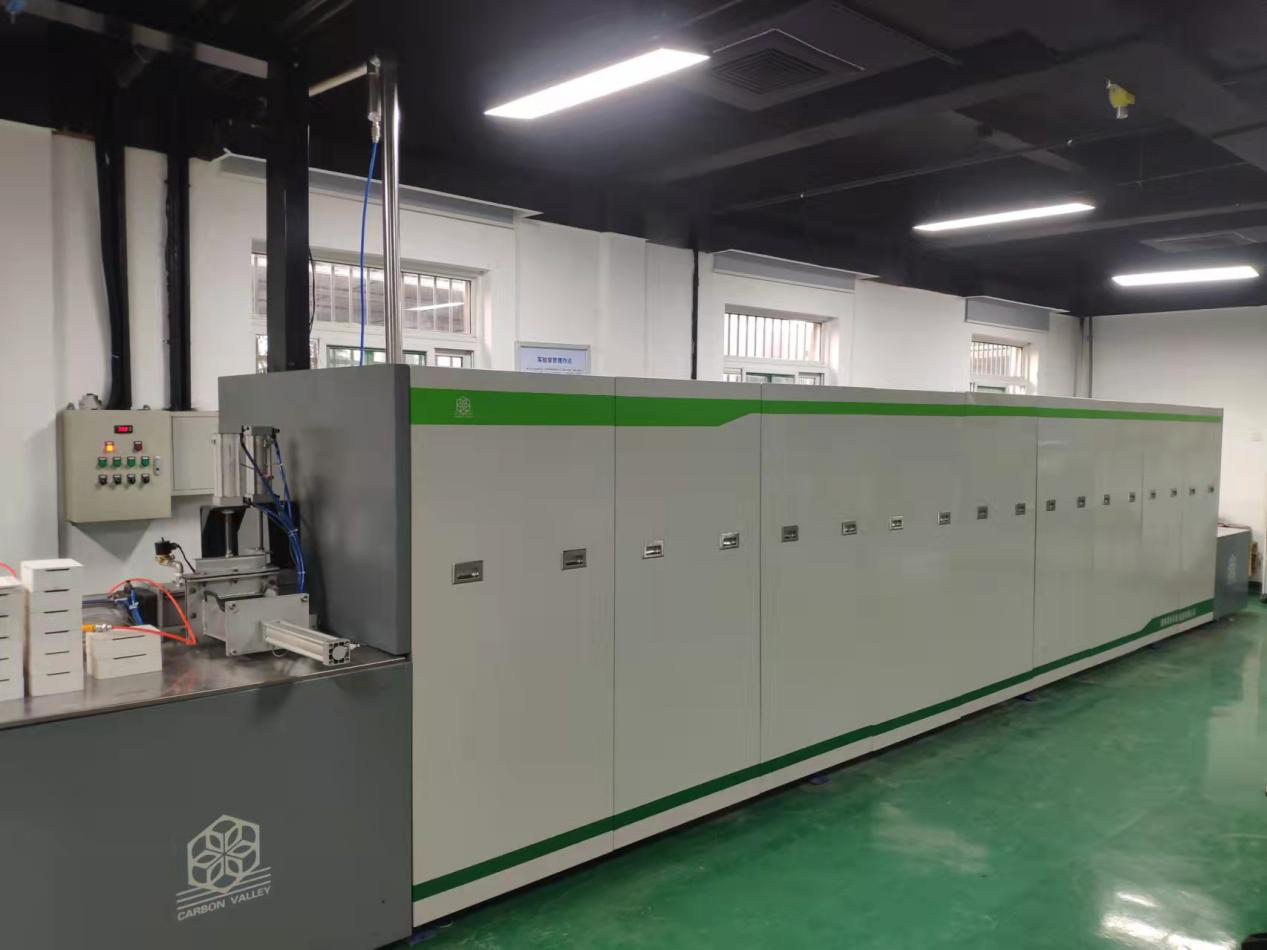
总之,提高高温回转窑窑内温度,提升生产效益,是当前工业生产领域亟待解决的问题。企业应从优化燃料燃烧、改进窑内结构、加强设备维护、实施智能化改造等方面入手,多管齐下,共同提高窑内温度。“《高温回转窑如何降低气压,看完你就知道了(全网更新)》”